
And if you take into account the large number of start-ups, short runs, and shut-downs that a new vehicle engine undergoes between the plant door and your driveway, getting rid of that contamination in the engine oil as soon as possible is a smart idea. When it comes to the only two things actually replaced at a first service - the engine oil and filter - getting it done sooner rather than later ensures any small debris left over from the manufacturing process, such as casting sand, is removed. Wheel or driveline vibrations can also lead to deeper damage if ignored, and while you might think your warranty will cover it, this won’t include your time from the inconvenience of a longer repair. These can stay hidden until warranty coverage has expired good luck getting those covered. Water-leaks, as another example, if left unattended, can lead to future electrical failures.
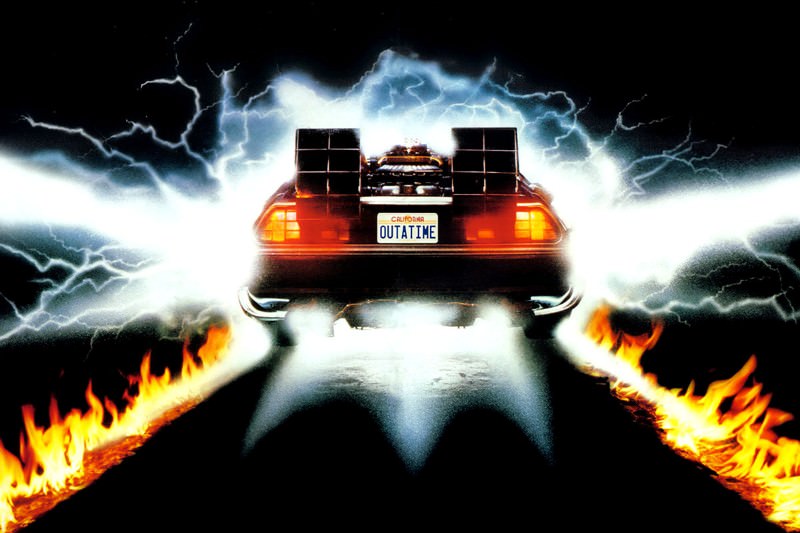
You definitely need to ask this at the service counter.
#Car time up update#
Different automakers handle software updates differently some can only take action if a specific complaint is registered others perform every update within warranty limits. A lot of on-board computer software updates fall into this category for example, you may not know that your infotainment system has a hidden flaw until your playlist is lost to the ages, or your GPS favourites suddenly become back roads in Outer Mongolia. The biggest benefit to an early first service is lessening the effects of any problems that might crop up, especially those missed by even the pickiest consumer. Article content Sweat the small stuff, even with a warranty The “wedding” is fully automatic and conducted by a robot that also bolts the front and rear axles to the body.This advertisement has not loaded yet, but your article continues below. The battery itself is connected to the body with 16 or 24 bolts around its perimeter (the number depends on the size of the battery) and four in the middle of the battery. This is the term used for the connection between the chassis and the body. The outcome is a finished chassis that is ready for the “wedding”. The “wedding” connecting the finished chassis with the body At this stage, a charging socket for later charging of the vehicle or electric motor – or two electric motors in the case of all-wheel drive ENYAQ iV vehicles – is connected to the battery and other components. As part of the chassis assembly, we connect everything up to form one functional unit,” explains Mulka. It contains the brake lines, the vehicle communication cable harnesses, the cooling lines for high-voltage components and the orange high-voltage harnesses. “We attach what’s known as a cable channel to the MEB battery – this connects the vehicle’s front and rear modules.

This work involves connecting the battery to other components. Use a circular motion to smooth the area. Then flatten the area using fine 2,500 grit wet and dry sandpaper or an abrasive paint cutting compound. “The chassis frame with the battery then proceeds down the line for subsequent assembly work,” says Josef Mulka, a BEV and PHEC specialist from the car production management department.Ī robot has placed the battery on the chassis frame. Now it’s time to apply the clear coat so that it is just a bit above the surrounding area, leaving the job to dry for about a day. So how does a battery weighing 500 kilos (that’s the weight of the 12-module version) become the heart of an entire electric car? On the production line where ŠKODA OCTAVIAs are made as well as the ENYAQ iV and ENYAQ COUPÉ iV models, the battery first comes into contact with a robot, which places it on the chassis frame. Chassis, wedding, bringing the car to life
